It is estimated that Indonesia produces approximately 7.8 million tons of plastic refuse a year (World Bank 2021). Very little of this plastic is recycled and much of it ends up in the ocean; after China, Indonesia is the biggest contributor to the world’s plastic leakage into the ocean, making up 10 percent of the world’s overall output.
While improved waste collection and management practices will be central to improving Indonesia’s plastic waste problem, so will the pursuance of a circular economy that minimizes plastic waste by recovering it and reusing it in innovative ways.
In response to this need, the USAID Indonesia Economic Growth Support Activity (EGSA) has been working on a formative study focused on Indonesia’s capacity to produce heavy-grade plastic sheeting using recycled materials. Plastic sheeting is one of the most widely distributed non-food relief items used in humanitarian operations. It is vital for helping families displaced by conflicts or whose homes have been damaged by disasters. Every year, hundreds of thousands of square meters of polyethylene sheeting are distributed by private-sector firms, non-governmental organizations, and government agencies to be used in disaster situations. This includes USAID’s Bureau for Humanitarian Assistance (USAID/BHA), which uses heavy-grade plastic sheeting to provide temporary cover for damaged roofs and walls or for other emergency applications as appropriate.
USAID/BHA currently uses a type of high-density polyethylene for this plastic sheeting, which it procures in the United States. Having a production center in Indonesia would allow USAID to strengthen its disaster response operations in the region by providing a more cost and time-efficient production alternative. This would be especially beneficial for Indonesia. In addition to potentially contributing to Indonesia’s recycling efforts, in-country high-density polyethylene sheet production would simplify disaster response operations in a country that is prone not only to tropical cyclones, but also to volcanic eruptions, earthquakes, tsunamis, and landslides due to its proximity to the Pacific “Ring of Fire.” The archipelago’s vulnerability to such hazards has been exacerbated by environmental degradation, including rapid deforestation and deteriorating watersheds.
The first phase of USAID EGSA’s research explored Indonesia’s capacity from a technology and capabilities stand-point to produce shelter-grade plastic sheeting. The research team discovered that Indonesia currently has 13 plastic sheeting manufacturers with a combined monthly production capacity of around 2,600 tons of tarpaulins. Given this, Indonesia could become a viable option for producing plastic sheeting.
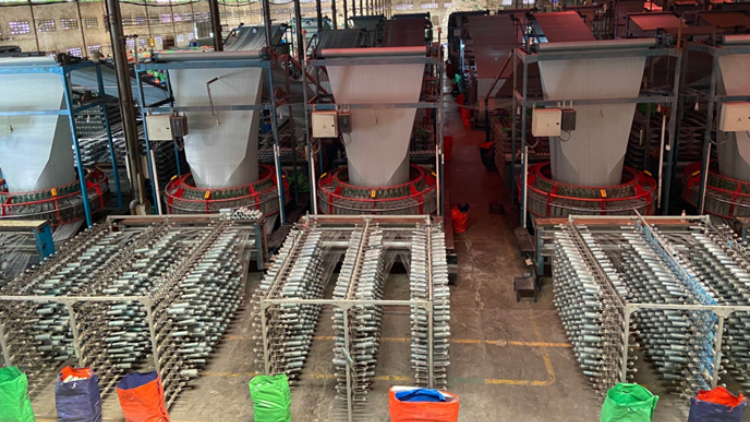
USAID EGSA’s first phase of research also focused on assessing Indonesia’s recycling capabilities. Specifically, USAID EGSA aimed to understand whether the country could feasibly convert recycled material to high-density plastic sheeting. The research team found that the country has the capacity to both use waste for plastic sheeting production as well as to recycle waste from the plastic sheeting production process.
The promising findings from this first phase of research have motivated USAID/BHA to commission USAID EGSA to conduct future studies on the market and financial feasibility of producing plastic sheeting in Indonesia. Specifically, the second phase of the study will focus us whether Indonesia can produce a product that is comparable to what is currently manufactured for USAID/BHA in the United States.
The Economic Growth Support Activity, implemented by DevTech Systems, Inc., aims to assist USAID to re-engage in economic growth programming in Indonesia. To learn more about EGSA and its year three results, read the EGSA Annual Report for Fiscal Year 2022.